
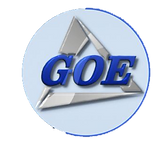
Innovative Spray and Slurry Systems
General Oil Equipment Co., Inc.
Call: +1 716 691-7012 or Email Us
Equipment
VPLS sprayers use proprietary dispersion drums to atomize and distribute liquid across the band. The speed of rotation controls the particle size and a variable speed pump controls the application rate. They are highly tolerant of particles in the liquid stream whether this is salt or product debris or suspended seasoning in slurries. They are direct drive to minimize bearings, seals and wearing components.
Depending on the application, there are several different versions including oil, high solids and very low flow. The dispersion drum has liquid distributed in the inner cavity by an inlet tube to create a wide spray pattern perpendicular to the belt and product travel. The raw spray pattern is modified by internal shrouding to create a uniform distribution across the band. This pattern is consistent over a wide turn-down on the pump speed.
Dispersion drums are flexible for a wide range of liquid applications and flow rates. Distribution uniformity is excellent to provide greater control and less product loss due to over application.
​
GOE’s equipment is build with:
Sanitary Design
GOE can build equipment to several sanitary design standards as required by the application. This includes BISSC (Baking Industry Sanitary Standards), GMA (Grocery Manufacturers Association), USDA, and 3A. The sprayer is considered a "wet-clean" area for sanitation.
Typical applications such as oil & sugar spray require BISSC and GMA standards. Spray on meat and cheese products or products with these components in them require USDA and 3A as well.
The equipment is designed to positively drain with no harborage areas. Liquid lines can be easily disassembled with tri-clamp and JIC fittings. Hinged covers provide access to the sprayer body and to the belt. Access doors in key locations provide additional points for inspection and/or manual cleaning.
Outside the spray area, we use paint-free motors and gear reducers wherever possible. Stand-offs are used to provide cleaning access and to minimize "sandwich" areas that can trap dirt or debris. Flat surfaces are eliminated wherever possible.
Product areas are polished with smooth and continuous welds. Outside the product zone, welds are continuous, but the surface finish is matched to the sanitary design and customer requirements.
​
Reliability
Equipment durability and reliability are essential in the VPLS design. Our reputation is based on experience with demanding and high volume production. We design for continuous duty to reduce costly equipment downtime.
We start with a heavy-duty frame and metal work that will not twist or otherwise deflect during installation or when the equipment is moved. Components are selected for reliability and our design emphasizes durability so the equipment and components are never running at design limits.
Less moving parts means less maintenance and this is a key design philosophy. We require fewer dispersion drums to apply liquid than competitive spinning disc units and they are all direct drive with reliable mechanical and lip seals. The dispersion drum drive motors are oversized to use larger bearings and shafts and they typically run at 1/3 of the full motor load capacity.
The sprayer belt is positive tracking using either sprockets or gears to drive and to maintain the belt position through the spray. This design is less likely to drift and to be damaged. The belt selection depends on the application.


